HEPA filters used in clean rooms and related test standards.
Prof. Dr. F. Taner Özkaynak
ABSTRACT
Usage of HEPA filters in cleanrooms is increasing rapidly, especially in the applications concerning food processing, pharmaceutical plants and hospitals. Basically there are two independent standards concerning the HEPA filters; CEN standards used in Europe and IEST Recommended Practices used in the United States. The filter efficiency is defined at 0.3 µm particle size for HEPA filters in IEST standards. In contrast, EN-1822 defines the filter efficiency at MPPS’s (Most Penetrating Particle Size). The filter test methods also differs in these two standards. IEST recommends particle counters and photometers for filter tests, while EN 1822 requires particle counters.
1. INTRODUCTION
According to the EN779 and EN1822 standards published by CEN (European Committee for Standardization) and used in European Union countries, air filters are classified into Coarse (G1, G2, G3, G4), Fine (F5, F6, F7, F8, F9), High Efficiency-HEPA (H10, H11, H12, H13, H14), and Ultra High Efficiency-ULPA (U15, U16, U17) categories. As known, G and F type filters are used in normal comfort applications and for the protection of high efficiency filters. This study will examine the standards related to high efficiency filters used in clean rooms, namely HEPA filters.
Clean room or clean environment applications are constantly increasing in our country, as in the whole world. The globalization in the pharmaceutical sector necessitates the production of products in environments compliant with existing standards for them to be marketed, thus popularizing clean room applications. Previously, HEPA (High Efficiency Particulate Air) filters, which were used only in A, B, C Class environments according to GMP rules, have started to be used as a standard in D Class rooms by some pharmaceutical companies in recent years.
2. IEST STANDARDS
The standards related to HEPA filters recommended by IEST are as follows:
- IEST-RP-CC001.3: HEPA and ULPA Filters
This standard explains the terms, classifications of HEPA and ULPA filters, definitions of materials used in manufacturing, test equipment, and marking methods.
- IEST-RP-CC034.1: Leakage Tests for HEPA and ULPA Filters
This standard describes the methods for leakage testing of HEPA and ULPA filters, test conditions, aerosol generation, aerosol detection methods (photometers or particle counters), and test methods.
- IEST-RP-CC021.1: Testing of HEPA and ULPA Filter Media
This standard explains the methods for conducting tests such as pressure drop, efficiency, thickness, strength, elongation, hardness, and weight loss at high temperatures for paper or synthetic materials used in the manufacture of HEPA and ULPA filters, as well as reporting techniques.
- IEST-RP-CC007.1: Testing of ULPA Filters
This standard describes the methods for efficiency testing of ULPA filters using particle counters.
In conclusion, the HEPA and ULPA filters defined by IEST and the recommended test methods are shown in Table-1.
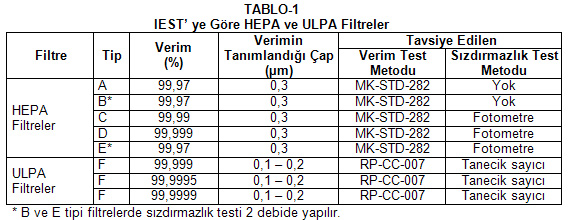
As can also be seen from the table above, HEPA filters are defined by their efficiency at a specific particle size (0.3 µm), while for ULPA filters, this size is smaller and given as a range (0.1 – 0.2 µm). Additionally, while leakage tests for HEPA filters can be conducted with the assistance of a photometer, more sensitive filters (ULPA) can be tested using particle counters.
3. EN 1822 STANDARD
The EN 1822 standard published by CEN consists of 5 parts, which are as follows:
- EN 1822-1 Classification, Performance Testing, and Marking
- EN 1822-2 Aerosol Production, Measurement Instruments, Particle Counting
- EN 1822-3 Testing of Filter Media
- EN 1822-4 Detection of Leakage in Filter Elements
- EN 1822-5 Efficiency Determination of Filter Elements
4. DIFFERENCES BETWEEN STANDARDS
Here, unlike IEST, MMPS (Most Penetrating Particle Size) is defined for efficiency rather than a fixed particle diameter, representing the most difficult-to-capture particle size. As known, HEPA and ULPA filters employ four different filtration mechanisms—electrostatic, interception, inertial, and diffusion mechanisms—to capture particles according to different physical rules. As the particle size increases, it enhances the inertial and interception effects while reducing the diffusion effect. Therefore, as can be seen from Figure-1, a particle size is selected for a filter media and a chosen velocity where capturing is the most difficult, and thus, efficiency is minimum (MPPS).
Şekil – 1
Çeşitli filtrasyon mekanizmalarının tanecik çapına göre verime etkisi ve MPPS.
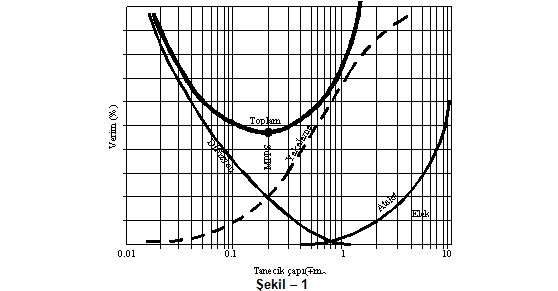
According to EN 1822, there are three different independent tests for HEPA and ULPA filters:
- Filter Media Efficiency Test: This is a test conducted at the airflow rate and MPPS (Most Penetrating Particle Size) typically performed by companies producing filter materials.
- Filter Leakage Test: This is a test conducted at MPPS using particle counters. However, for H13 and H14 filters, an alternative oil smoke leakage test may also be applied.
- Filter Efficiency Test at MPPS: This involves determining the total efficiency of the filter using a fixed probe and associated particle counter, or by scanning the entire filter surface.
Another difference between IEST and CEN standards is the method used for leakage testing. As can be seen from Table-1, while IEST recommends the use of photometers and particle counters depending on the filter type, EN1822 only recommends particle counters or Differential Mobility Particle Sizers (DMPS) and does not recommend photometers.
Furthermore, EN1822 allows for the determination of filter efficiency using the same values while conducting surface scanning for leakage testing. This method allows for both leakage and efficiency to be determined simultaneously, which is not present in IEST.
Finding the exact equivalents of the filter types defined in IEST (A, B, C, D, E, F) in EN-1822 can be quite challenging. Since MPPS and efficiency vary according to velocity, velocity becomes an important factor. For example, a filter classified as H14 according to EN1822 at a certain velocity may correspond to a class C in IEST, but as the velocity increases, the filter may still meet the requirements of class H13 according to EN1822 while still meeting the requirements of class C according to IEST.
In addition to the mentioned standards, regulatory authorities may have specific requirements as well. For example, in the United States, the most renowned regulatory agency, the FDA (Food and Drug Administration), only allows the use of photometers for leakage testing in areas where HEPA filters are used. Additionally, in tests conducted in sterile environments, the use of solid particles is not permitted by the FDA.
Generally, apart from efficiency and leakage, other desired properties of HEPA filters include minimal pressure drop, uniform airflow distribution across the surface, absence of gas emissions from materials used in construction, easy installation and removal, long lifespan, and resistance to moisture.
5. BIBLIOGRAPHY
[1] ÖZKAYNAK F.T., “Clean Room Design and HVAC Systems”, Tetisan Technical Publications, 2001.
[2] IEST, “IEST-RP-CC001.3 HEPA and ULPA Filters”, 2003.
[3] IEST, “IEST-RP-CC034.1 HEPA and ULPA Filter Leak Tests”, 2003.
[4] IEST, “IEST-RP-CC021.1 Testing HEPA and ULPA Filter Media”, 2002.
[5] IEST, “IEST-RP-CC007.1 Testing ULPA Filters”, 2002.
[6] CEN, “EN 1822-1 Classification, Performance Testing Marking”, 1998.
[7] CEN, “EN 1822-2 Aerosol Production, Measuring Equipment, Particle Counting Statistics”, 1998.
[8] CEN, “EN 1822-3 Testing Flat Sheet Filter Media”, 1998.
[9] CEN, “EN 1822-4 Determining Leakage of Filter Elements (Scan Method), 2001.
[10] CEN, “EN 1822-5 Determining the Efficiency of Filter Elements”, 2000.
Author
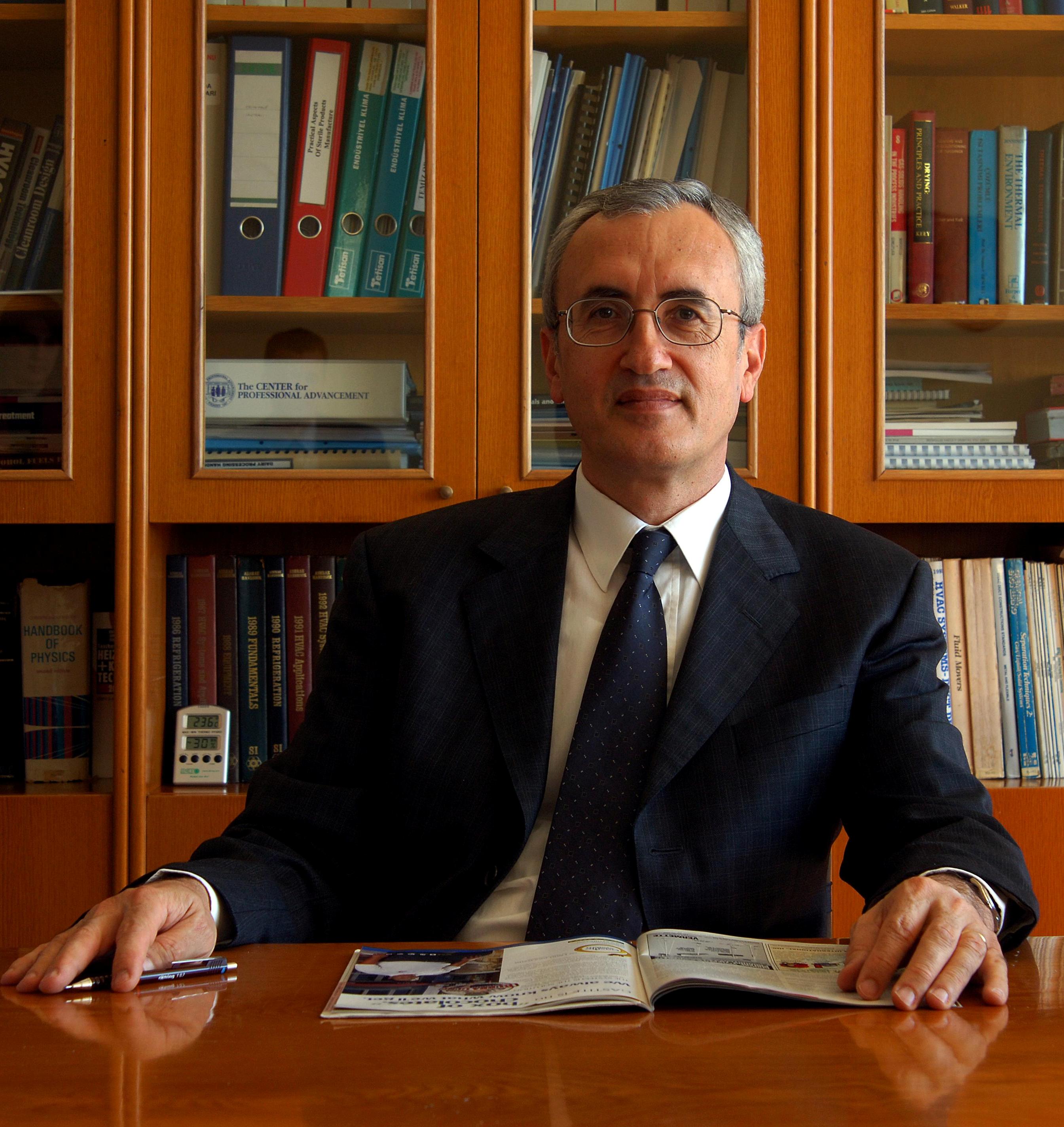
After attending high school at Robert Academy, he graduated from Istanbul Technical University (ITU) as a Mechanical Engineer in 1971. He obtained his Ph.D. from Lehigh University in the United States in 1974, became an Associate Professor in 1981, and was appointed as a full Professor at ITU Faculty of Mechanical Engineering in 1995. In addition to his academic career, he has been involved in various projects for organizations such as General Electric (GE), the Atomic Energy Commission (AEC), and the Energy Research Center (ERC) in the United States. He has managed projects and contracts in various fields including industrial and cleanroom HVAC systems, drying, heat recovery, flue gas cleaning, pneumatic conveying, and purification. While continuing his partial status as a faculty member at ITU Faculty of Mechanical Engineering, he also served as a manager at Tetisan Ltd. Company. Prof. Dr. F. Taner Özkaynak has published over 35 articles and books on various subjects. He was one of the founders of Ulpatek Filtre and passed away on October 20, 2011.
F.Taner ÖZKAYNAK,