CURRENT STANDARDS IN AIR FILTRATION
ISO 16890 standard is the new standard that has replaced the EN779: 2012.
This standard covers Coarse filters (Class G), Medium filters (Class M) and
Fine filters (Class F) and eliminate the insufficient points of the old standard.
With this change in standard, filter users will be able to choose the filter
much more accurate according to their needs. ISO 16890 standard considers
for the particle size (Particulate Matter = PM) between 0.3 μm and 10 μm for
efficiency evaluation. Filters are divided into 4 groups.
ISO 16890 Classifications
ISO ePM1
ePM1 95%
ePM1 90%
ePM1 85%
ePM1 80%
ePM1 75%
ePM1 70%
ePM1 65%
ePM1 60%
ePM1 55%
ePM1 50%
Requirement
≥50% Initial Efficiency
≥50% Discharged Efficiency
ISO ePM2,5
ePM2,5 95%
ePM2,5 90%
ePM2,5 85%
ePM2,5 80%
ePM2,5 75%
ePM2,5 70%
ePM2,5 65%
ePM2,5 60%
ePM2,5 55%
ePM2,5 50%
Requirement
≥50% Initial Efficiency
≥50% Discharged Efficiency
ISO ePM10
ePM10 95%
ePM10 90%
ePM10 85%
ePM10 80%
ePM10 75%
ePM10 70%
ePM10 65%
ePM10 60%
ePM10 55%
ePM10 50%
Requirement
≥50% Initial Efficiency
≥50% Discharged Efficiency
ISO Coarse
ePM10 45%
ePM10 40%
ePM10 35%
ePM10 30%
ePM10 25%
ePM10 20%
ePM10 15%
ePM10 10%
ePM10 5%
No discharge requirement
EN 1822
Efficiency Particulate Air Filters (EPA), High Efficiency Particulate Air Filters (HEPA) and Ultra Low Penetration Air Filters (ULPA) classified and tested according to EN 1822 standards. These filters are used in many industries including, pharmaceutical manufacturing, Bio-Tech,Electronics, Aerospace, Hospitals, and more.
There are independent tests for EPA / HEPA / ULPA class filter and filter media according to EN 1822.
1. Efficiency test of the filter fiber: An efficiency test performed by the filter material manufacturers at the nominal speed and MPPS.
2. Filter leak test: It is the test done at MPPS by using particle counters. An alternative to this test is the oil smoke leakage test for H13 and H14 class filters.
3. Filter efficiency test at MPPS: A method of measurement by scanning the filter surface under test conditions. Efficiency is measured with the particle counters used in this test.
MPPS: Most Penetrating Particle Size
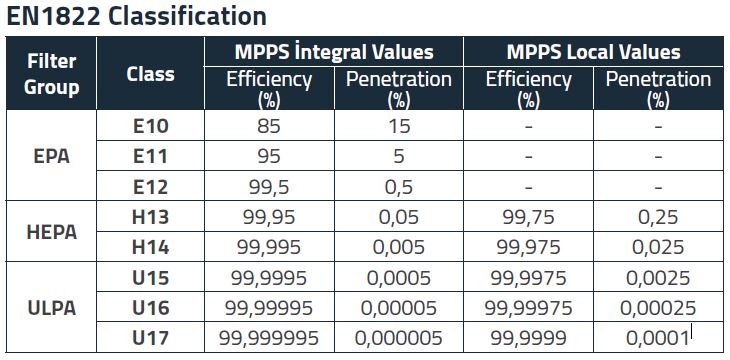
PERFORMANCE TEST SYSTEM - PTS 5002
Used performance measurements for different model and different efficiency of filters .
• The pre-tests of the new designs are carried out after than the design giving the best results replaces the standard product.
• Comparison tests of filters which has the same efficiency but made from different raw materials.
• Air flow and pressure drop graphs are prepared by measuring the initial pressure drop values of the filter at different rated air flow.
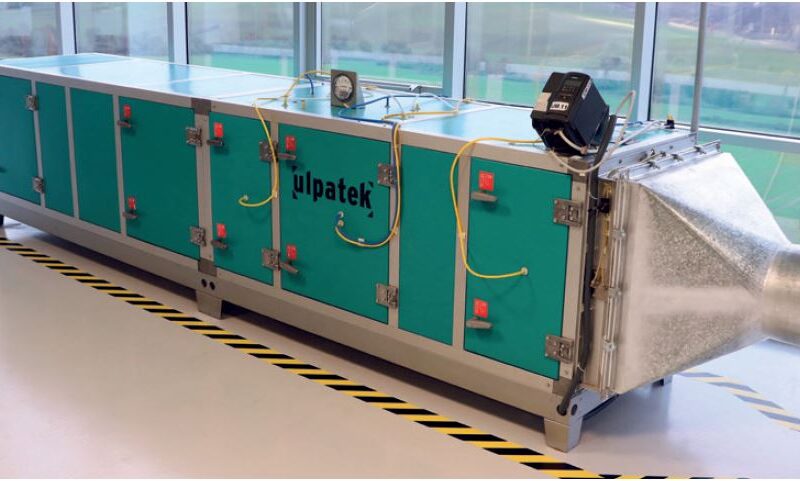
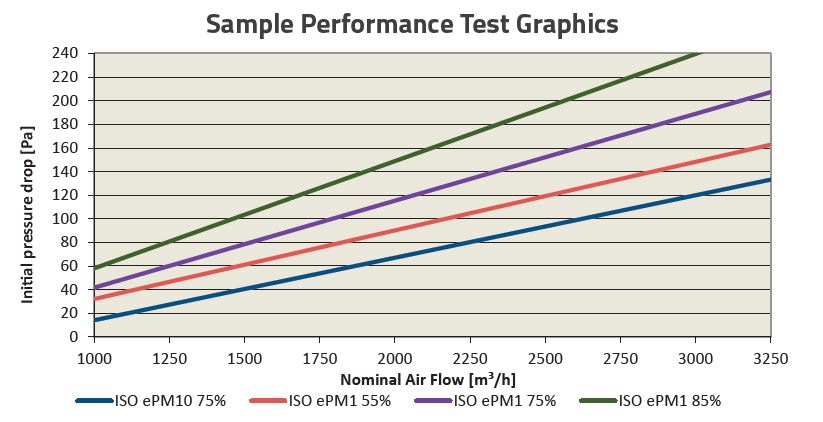
FILTER MEDIA TEST SYSTEM - FMT 102
Used measuring the raw material’s filtration efficiency and initial pressure drop values at diffirent air velocities.
• Different oils (Emery 3004, Paraffin etc.) and salt (NaCl) can be used as the source of liquid and solid aerosols in the tests.
• Pre-tests are made for raw materials manufactured by different suppliers to make detailed comparisons. The selection of the best quality raw materials is supported by the test results obtained here.
• Raw material quality control tests are carried out with this system before production.
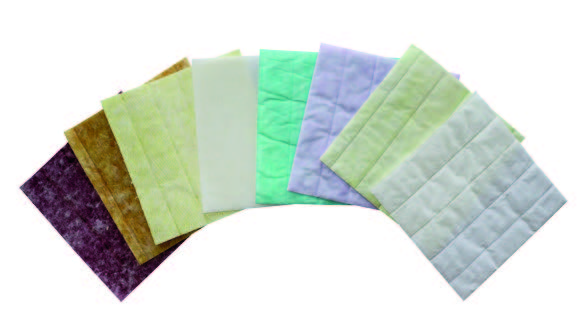
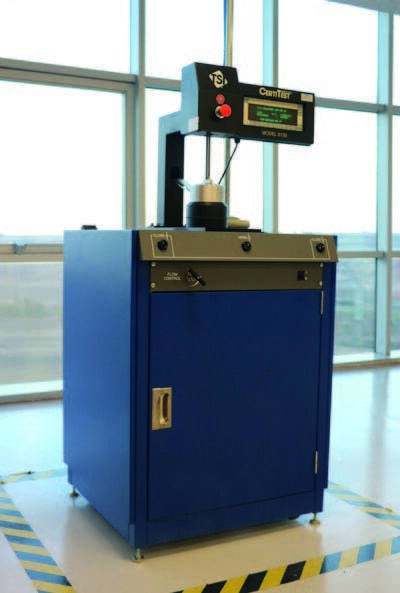
ISO 16890 TEST SYSTEM - FTS 3401
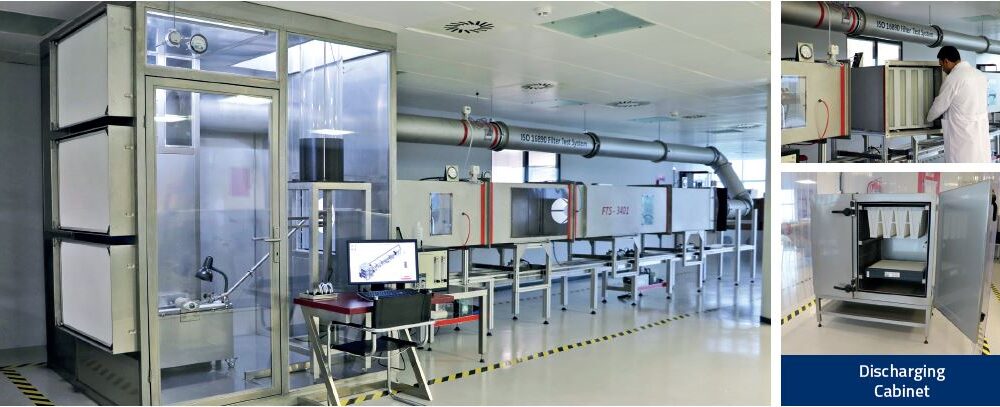
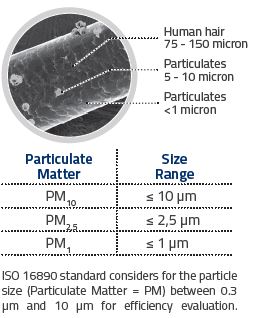
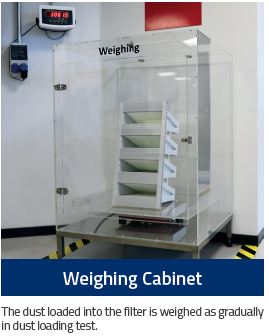
ISO 16890 Test Procedure Step By Step
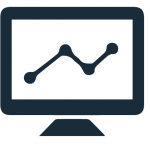
Step 1
Test procedure of the ISO 16890 standard begins with measuring the efficiency of an air filter at a particle size range of 0.3 μm to 10 μm.
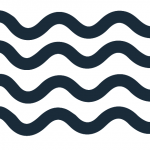
Step 2
The Filter is subjected to an isopropanol vapor atmosphere to eliminate efficiency of electrostatic mechanism.
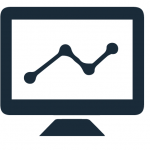
Step 3
Isopropanol vapor atmosphere conditioned Filter tested again to measure the minimum efficiency ePM1,min and ePM2,5,min
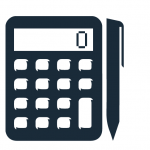
Step 4
Efficiency for each PM size is calculated by the mean of both conditioned and the conditioned filter.
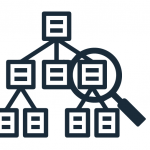
Step 5
The efficiencies for ePM1 are calculated for the particle size 0,3 -1 μm , ePM2,5 for the particle size range of up to 2,5 and ePM10 for the particle size range of up to 10 microns.
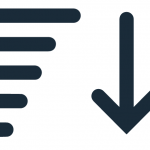
Step 6
Calculated efficiency values are rounded to the nearest lower value according to the efficiency values in the ISO 16890 classification groups.
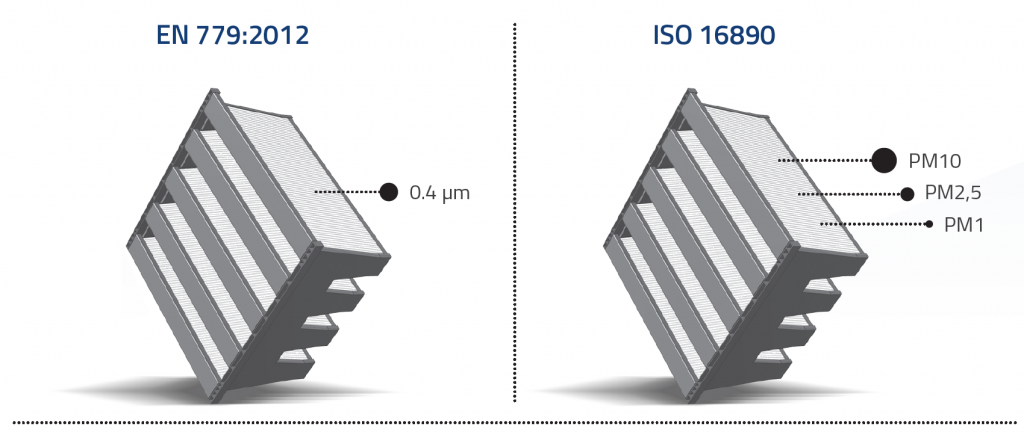
For example; According to the test result, the F8 class V-Compact Filter is classified as “ISO ePM1 70%”. This means that the filter seperates %70 of PM1 particles. The “e” stands for efficiency in combinition with the particulate matter (PM).

Some details about ISO16890
Efficiency is given according to PM10, PM2,5 and PM1.
The dust holding capacity is calculated for ISO A2/AC Fine synthetic test powder.
Initial gravimetric arrestance efficiency is calculated.
The filter differential pressure drop (Δp) is measured at the nominal air flow rate.
For efficiency evaluation, the particle size is between 0.3-10 μm.
The efficiency is measured separately according to the particle range.
The efficiency measurement is repeated 24 hours after the IPA process.
The «ePMx efficiency» is calculated with the measured efficiencies.
The filter performance is determined according to PM10, PM2.5 and PM1.
Seperately efficiency results in each particle channel.
The process is considered when selecting the filter.
Global (ISO, International Organization for Standardization).
HEPA / ULPA FILTER TEST SYSTEMS
CEN standards in Europe, IEST and MIL standards in the US are used for HEPA and ULPA filters. HEPA / ULPA filters are individually tested and certified in accordance with both standards in Ulpatek.
HUF-SCAN 4002
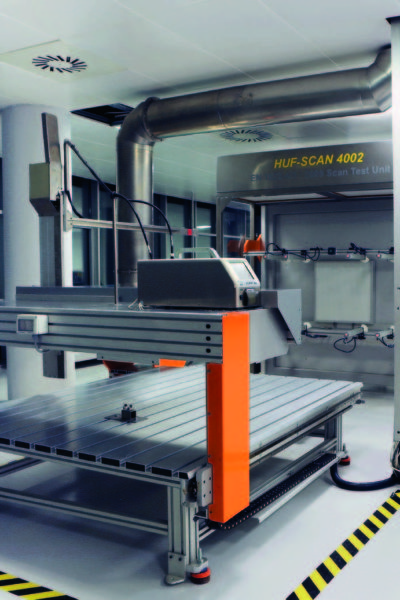
HF-SCAN 3004
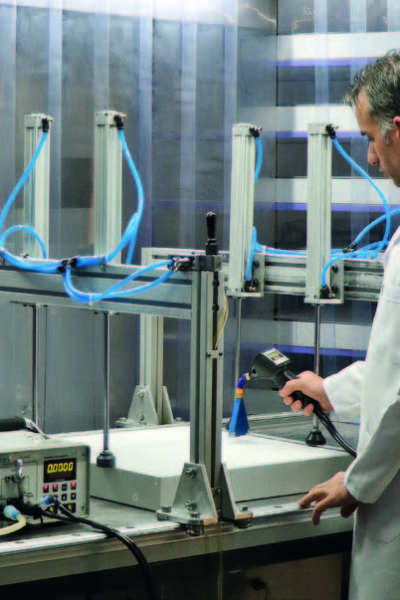
HF-OIL MIST 1200
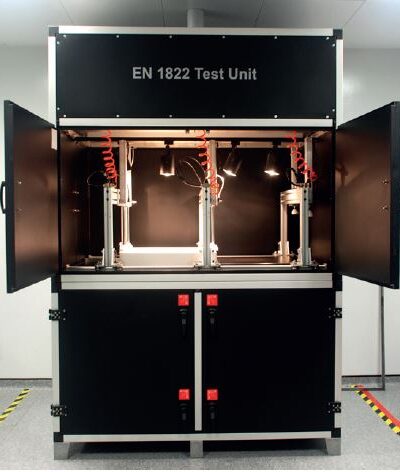
In the system, the filter surface is scanned at nominal air velocity by automatic probe which counts particles at MPPS by connecting particle counters counters are connected at MPPS and nominal air flow rates.
• Aerosol concentration is counted by the particle counters before and after the filter during test.
• It is a test method in which the lowest penetration value which is accepted according to the filter class is checked in Class 100. If there is a leak, it detects the leakage points and print as a figure.
• Scanning test is the most advanced filter efficiency test used to test HEPA and ULPA filters
Test operator scans the filter surface with the probe which is connected to photometer to check the leakage at 0,3 μm particle size. Test is applied for each filter individually.
• In the leak tests of HEPA filters performed at the nominal air flow rate, aerosols such as Emery 3004, PAO etc. are used according to standard.
• The high concentration of aerosol fed during the test is checked in the Class 100 test area by scanning the filter surface and sealing surface with the probe to check leakage.
• If there is leakage, repairing can be carried out by applying special adhesive according to the standard and customer requirements to the leakage point.
• After installation of the filters in the field, performing this test is recommended before commissioning system.
Oil Thread Leak Test is done by naked eye for checking leakage on the HEPA filter surface at a nominal air flow rate using DEHS as aerosol.
• The particles formed as oil smoke lines from their leak points can be easily seen with the black colored cabin interior design and the appropriate light angle.
• If there is leakage, repairing can be carried out by applying special adhesive according to the standard and customer requirements to the leakage point.
• Used as an alternative leak test method for class H13 and H14 class filters.
• It provides easy testing for filters which are not suitable for the scanning test (V-Compact, cylinder filter, filters without faceguard protection).